A Comprehensive Guide
HOLLOW WOOD SURFBOARDS
Build Hollow Wood Surfboards with AkuShaper
Download files from Akushaper to get started.
There’s nothing quite like riding a surfboard you’ve built yourself — especially when it’s crafted from sustainably sourced wood. Hollow wooden surfboards combine timeless craftsmanship with modern design tools, giving you a hands-on, environmentally conscious way to connect with surfing from start to finish.
Whether you’re a backyard builder or an experienced shaper, AkuShaper makes it easier to bring your vision to life. You can precisely design internal structures, outline curves, rocker profiles, and volume distribution — all while planning your build around the unique behavior of timber.
But not all wood is created equal. Different species of timber vary in strength, weight, cost, availability, and how they react to moisture and bending. Before you start your build, it’s important to research your timber options. Consider factors like:
Density and buoyancy
Grain consistency
Resistance to saltwater
Regional availability and price
How the wood will handle shaping, gluing, or bending into curves
From red cedar and paulownia to recycled planks and locally harvested lumber, your choice of wood will shape both the look and the performance of your board.
On this page, we’ll explore how AkuShaper supports every step of the hollow wood board-building process — from planning internal chambers and outlines to printing custom templates and adjusting for material thickness. Whether you're designing a traditional fish, a classic single fin, or a modern mid-length, this is your complete guide to combining precision software with natural materials.
CK Surfboards - Ireland
“If you’re looking to design something unique, AkuShaper will definitely help you reach your full creative potential.”
“Using Aku shapers hollow wood board software to design my hollow wood surfboard was an absolute game-changer. The software’s intuitive interface made it easy to bring my vision to life, allowing me to focus on creativity rather than getting lost in technical details. The tools for adjusting dimensions and visualizing the internal structure were simple, yet powerful, and helped me push my design to new heights.”
“It really allowed me to explore and experiment without limits, and the 3D previews gave me confidence in every decision. With great support and tutorials, I was able to quickly generate detailed plans, saving time and frustration in the workshop.”
Three Main Design Pathways in AkuShaper
No matter your tools or experience level, AkuShaper gives you flexible options to bring your hollow wooden surfboard to life. Whether you’re cutting by hand in your garage or exporting files to a CNC machine, you can start with a precise digital design and move seamlessly into physical construction.
Here are the three main ways to use AkuShaper for hollow wood surfboard building:
1. Print Full-Size Templates for Hand Cutting
Perfect for traditionalists and DIY builders, AkuShaper lets you print full-scale templates directly from your digital design. These include:
The board’s outline
Rocker profile (side view)
Cross-sections or slices of the board
You can glue these paper templates to your timber stock or plywood sheets and cut everything by hand using a jigsaw or bandsaw. It’s an accessible, low-cost method with high precision — great for first-time builders or anyone who enjoys hands-on craftsmanship.



2. Export DXF, IGES, or STL Files for CNC Cutting
If you have access to a CNC router or laser cutter, AkuShaper allows you to export your board’s outline, rocker, and internal slices in industry-standard formats like DXF, IGES, or STL. This makes it easy to:
Cut accurate ribs and stringers
Nest parts efficiently on your material sheets
Scale up production or experiment with multiple prototypes
It’s ideal for schools, workshops, or experienced builders who want the repeatability and speed of CNC tools — while still working with beautiful natural wood.

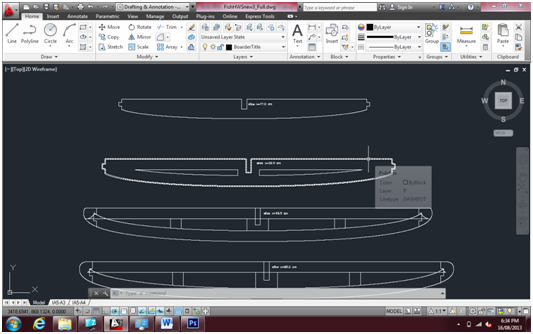

3. Use HBTM (Hollow Board Template Maker) with Aku Files
For those building frame-style hollow boards, the Hollow Board Template Maker (HBTM) plugin works seamlessly with AkuShaper files. With just a few clicks, you can convert your Aku file into a detailed internal skeleton layout — including:
Precise frame ribs
A center stringer
Slot and tab joints for assembly
This approach offers the best of both worlds: modern digital design and efficient template generation, with a finished board that’s light, strong, and stunning.
Please visit this page to download the Hollow Board Template Maker: https://help.akushaper.com/category/18-hollow-wood-surfboards



Construction Types
Hollow Wood Construction
Timber ribs and centre spine, outer rail strips, either narrow strips, flat rocker shaped pieces or our Stacked Rail Method with timber skins. Perfect for the DIY Builder, with little to no experience. Requires a vent.
-
This type of board is hollow and has a solid timber or plywood internal frame, consisting of a centre spine and horizontal ribs, then clad with timber.
If choosing a fibreglassed finish with this type of build, the deck and bottom timbers can be 6mm thick. As the fibreglass provides structural integrity to the board. Internal ribs are spaced to suit the size of the rider, usually about 120mm to 150mm apart. Closer together where the rider will be standing.
If you're going for an oiled or varnished finish, you will need at least 8mm thick deck and bottom timbers. The spacings of the ribs will need to be closer together to support the rider adequately. Usually 100mm apart where the rider will be standing. Varnish and oiled finishes will provide zero structural integrity to the board.
Pros - Minimal experience can produce an excellent result - Less expensive tools required compared to other methods.
Cons - Will flood with water if badly dinged - Must have a working vent otherwise the board will over pressurise and split.
Bow Frame Construction
Sturdy timber outer frame with ribs giving support through the centre. Timber skins. Not as popular as the other methods, requires a rocker shaping table and shaping knowledge. Requires a vent. Can be made by the advanced DIY builder.
-
Similar to the Hollow Construction, this type of board is also hollow but doesn't have a centre spine, just horizontal ribs. Positioned to suit the riders weight, usually about 100mm to 120mm apart where the rider would stand.
Ribs can be made from either solid timber or plywood, it has a solid rail around the perimeter which gives it its strength, clad with an outer timber skin.
If choosing a fibreglassed finish with this type of build, the deck and bottom timbers can be 6mm thick. As the fibreglass provides structural integrity to the board. If you're going for an oiled or varnished finish, you will need at least 8mm thick deck and bottom timbers. The spacings of the ribs will need to be closer together to support the rider adequately. Usually 100mm apart where the rider will be standing. Varnish and oiled finishes will provide zero structural integrity to the board.
Pros - Minimal experience can produce an excellent result
Cons - Will flood with water if badly dinged - Must have a working vent otherwise the board will over pressurise and split
Chambered Construction
Sections of timber cut to the rocker shape, tack glued then roughly shaped. Separated hollowed out glued back together. Then final shaping. Requires a vent. DIY builders do make them, there's lots of waste timber and some shaping knowledge is required.
-
Unlike other construction methods this one requires a good amount of knowledge about shaping, it's similar to how board makers shape foam boards with all of the shape done by hand. While other methods has the shape is built in to it, this one is all done by eye.
This type of construction can be either fibreglassed, oiled or varnished. The structural integrity that glassing can provide is not a big factor here as these types of boards usually have solid structure.
Another factor to consider is that this construction method is very solid with little to no flex and is generally heavier than other methods.
Pros - Produces a stronger board - Less tools required compared to other builds.
Cons - Can result in a heavier board than other methods - Time consuming build.
Foam Core Construction
Shaped foam core with timber rails and timber skins. This one is the easiest and quick method to build, does require knowledge of shaping, doesn't require a vent and won't flood with water if badly dinged.
-
This composite type of construction relies on the vacuum bagging of a timber foam timber sandwich to create its strength. A commonly used system in the building industry it forms a very strong board.
This type of construction can be either fiberglassed, oiled or varnished. The structural integrity that glassing can provide is not an important factor here.
Pros - Lightest and strongest of all the build methods - Quick build.
Cons - Requires more expensive equipment - Can delaminate if left in a hot environment for log periods of time.